石原ケミカル 株式会社・滋賀工場 様
”送り状レス”システムで省人化
1千万円ものコストダウンとサービス向上を達成
鉛フリーめっき液でトップシェアの石原ケミカル株式会社様。2000年にハンディターミナルによるバーコード検品システムを刷新した同社は、このほど送り状発行業務を全面的に見直し大きな成果を上げた。
お客様満足にも繋がった「送り状レス」システムを詳しくご紹介する。
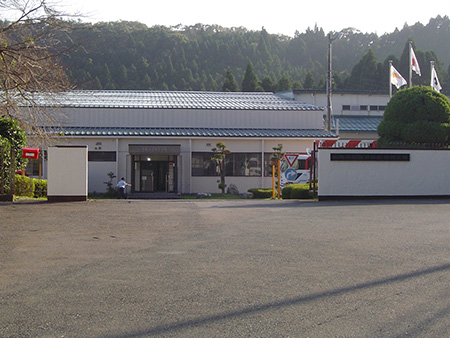
石原ケミカル株式会社は1900年の創業以来1世紀余、界面化学技術をベースに、工業薬品や自動車用化学製品のメーカーとして確かな足取りで成長してきた。だが近年はハイテク業界の発展に伴い、ニッケル超微粉、ポリイミド樹脂などの電子材料・機器分野、さらにデジタル家電用のコンデンサ、ICチップなどの生産に使われるハンダめっき液など金属表面処理剤の事業が大きく伸張。中でも鉛フリーめっき液は、環境負荷低減が企業の重要課題としてクローズアップされる中で需要が急拡大。国内トップシェアを獲得し、5期連続増益で今期も過去最高益を更新する勢いだ。他に先んじて高付加価値の製品を世に送り出す、研究開発体制の充実がその勝因だろう。
今回編集部が取材に訪れた同社の生産拠点・滋賀工場は、琵琶湖の南西端から西岸をぐっと北上した滋賀県高島市にある。構内に設置された物流センターが担う物流業務のイメージを確かめておくと、大半が液体薬剤となる同社製品の出荷荷姿は主に段ボールケースまたは缶入りで、拡大中の輸出用製品はポリ容器入り。いずれも1ケース・1個分の重量は20㎏前後。
これらの物流関連業務を統括するのは、受注などデリバリー業務から入出庫・入出荷など物流センター現場業務までを司る同工場の物流課。既に2000年にハンディターミナルによるバーコード出荷システムを導入し、誤出荷を激減させた実績を持つ。だが以後数年を経て、新たなユーザーニーズへの対応課題や、さらなる現場効率改善をテーマに掲げ、同課では05年から06年にかけ、2つのステップによる新たな改善活動に取り組んだ。
いずれもシステム構築パートナーに選定したユーザックシステムの全面協力を得て、プロジェクトは成功裏に完了、日々の業務に大きな改善効果をもたらしている。 本ケース・スタディでは、その改善プロセスとシステムポイントにフォーカスすることにしたい。
2ステップの改善活動
1.ロット管理システムの導入
物流課が今回、まず第1ステップとして取り組んだのは、導入後7年目を迎えていたハンディターミナルの刷新と合わせ、ロット管理システムを構築することで、05年10月に稼働を開始した。それまで製品のロット管理は担当者が台帳に記入する方法で対応していたのだが、「これには年間14,400分、つまり1日1時間前後を要していました。万一問題が発生し特定ロットの製品がどこに納品されたか調べるには、分厚い台帳をひっくり返して探すほかありませんでした」と改善プロジェクトの中心者である物流課受注係の村井健治リーダーは話す。
そこで新システムは、製品ラベルに従来のアイテム識別用JANコードのほか、日付・ロット情報もCODE39のバーコード化して貼り付ける方式とした。入出庫時にこれらの2段バーコードを新しいハンディ端末で読み取るだけで、製造ロット単位でどの製品を・いつ・どこに出荷したか記録するトレース管理が可能になった。
先入れ先出しにも対応するほか、問題発生時のロット検索はパソコンへの条件入力で瞬時に調べられる。それでも台帳記入作業は全く不要に、つまり14,400分が0分へと削減されたのだ。
2.送り状レス化の着眼点
引き続き第2ステップとして「送り状レス」のシステム構築に挑戦。こちらは06年8月から本稼働を開始したばかりだ。物流課でこれまで取り組んできた改善は出荷現場が対象だったことから、今回は女子従業員の多い受注工程に着目。単純作業の中にも効率化すべきテーマがあるはず、とにらんで調べてみた。すると、もっとも時間のかかっている単純作業は「送り状と荷札のセット」で、これには月間9,600分も要していることが分かった。
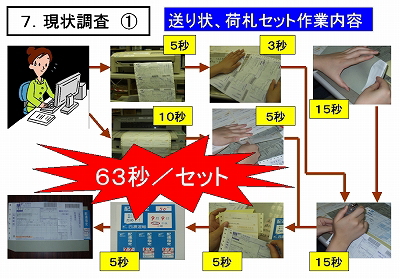
作業の流れは、プリンターから連続帳票で出力される送り状を手作業でカットし、出荷単位(ユーザー別)にまとめホチキス止め、さらに荷札と、配達指定ラベルに日付を書き込んでからこれらをセットするもの(図表-1)。1セット当たり平均所要時間は63秒だ。 また担当者にヒヤリングしてみると、この時誤配送を防ぐため、送り先と印字内容を照合確認することも非常に大事なことが分かった。 比較的勤続年数が短く女性・新人が多いという職場特性の中で、単純だが反復作業で時間がかかり、ミスを起こしやすい業務になっていたということだ。
村井リーダーは、「宛先確認の他にも、お客様の依頼でその会社の社名・住所を押印するOEM送り状もあるなど、単純な中にも種々の判断が要求される作業になっていました」と指摘する。 「そこでこれらをシステム的にカバーできないかと考えたんです」
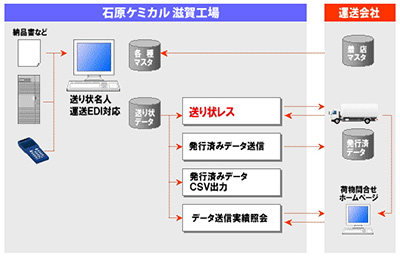
従来は送り状、荷札の出力用に6台のプリンターを使っていたが、オフコン用プログラムで動いていたため、こうした要望を反映するフレキシブルな運用変更は難しかった。 そのため村井リーダーらはパソコンベースの適切なシステムがないかと展示会、専門誌やインターネットなどを調べ、探し回った。こうしてある日見つけたのが、ユーザックシステムのパッケージシステム「送り状名人」だった。本システムの構成は、図表-2のようなイメージ。しかしパッケージシステムをそのまま導入するのではなく、ベンダーや関係者と5か月にわたり打ち合わせを重ね、最適な仕組みを作り込むことにした。そのポイントを、次項で述べよう。
新システムの工夫ポイント
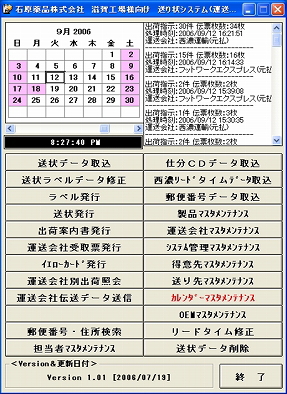
1.送り状と荷札のセット作業をなくす
「送り状と荷札のセット」という改善テーマの根本的解決法は、セット作業自体をなくすことだ。「送り状なし・荷札だけ」で配送できれば手間はないのだが、運送会社に打診すると「それは無理」との回答。しかし新システムの機能を活用し、送り状データをEDIで運送会社に送信すれば(図表-3)、石原ケミカルが行っていた送り状発行を運送会社が代行することは可能と分かった。 そこで石原ケミカルは荷札だけを貼って出荷する、送り状は運送会社が発行し集荷後に荷物と照合する、という「送り状レス化」を断行、ホチキス止めを含むセット作業もなくすことに成功した。
これに伴い荷札には、従来のセット作業時に別のラベルに手書きし貼っていた配送指定日時をリードタイム計算により自動印字、ドライバーが手書き記入していた着店コードも印字されるようにした(写真-1、2)。またOEM送り状への顧客住所押印も自動印字で、双方の手間と作業ミスを皆無とした。
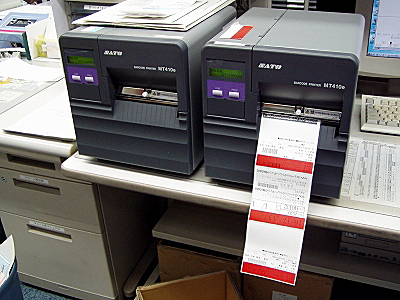
写真-1:2台のプリンタから荷札を出力
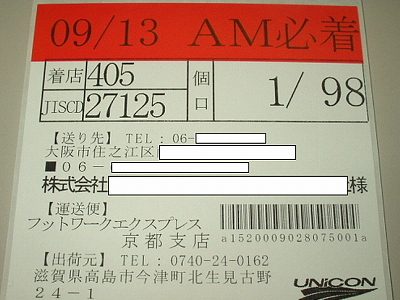
写真-2:配送日時指定と着店コードも自動印字
これらの判断・付帯作業自動化で、未経験者でも正確・迅速な作業が可能になった効果は大きい。 加えて運送会社側では、それまで石原ケミカルの発行した送り状からデータを手入力していたのだが、この負担が一切なくなるとともに、EDI情報が事前に受け取れることで集荷トラックが戻る前にターミナルから各方面への出荷量を把握し段取りできるようになるなど、波及効果が生まれている。
2.荷札のカット作業をなくす
次に、セットをなくしても残る手間の1つとして、連続帳票のミシン目のカット作業がある。誰でもできる簡単な作業ではあるが、「簡単だから自動化したい」というのが村井リーダーの発想だった。 ベンダー担当者に相談した結果、2台の新プリンターにカッターを取り付け、システムに連携しユーザー別の区切りで自動カットできるようにした。これで顧客ごとの出荷単位別荷札まとめ作業の手間とミスを撲滅できた。
3.配送状況問い合わせへの対応
商品を注文した顧客から「いつ届くのか」「いまどこにあるのか」といった配送状況問い合わせが増えているのは、多くの業界共通の悩みだ。従来は顧客から問い合わせ電話があると、受注係が伝票控えを調べ、社内の伝票番号に対応する運送会社の送り状の問い合わせ番号を確かめ、運送会社のWebサイトで確認する必要があった。
そこで今回は両番号をシステム的に紐付けし、伝票番号を入力するだけで運送会社のサイトで配送状況確認ができるようにした(図表-5)。
「お客様からの配送問合わせ電話は1日に10~20件程度ですが、あれこれ調べていると1件当たり10分近くの処理時間がかかっていました」と村井リーダー。
「そこでユーザックのシステム画面をカスタマイズして、伝票番号入力から1クリックで配送状況画面に飛んで検索できるようにしてもらいました。これで大幅に対応時間を短縮し、顧客サービスを向上できたと思います」
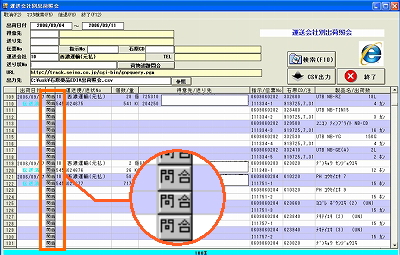
システム導入の効果
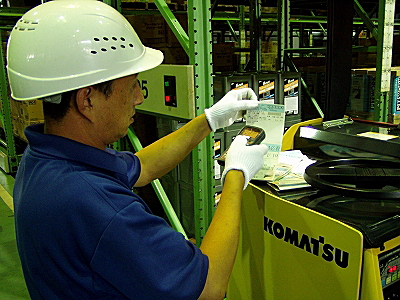
新システムによる出荷作業の流れを見ておこう。出力された荷札を出荷作業者が受注係の事務所から受け取ると、作業者はまず荷札のバーコードをハンディ端末でスキャンするとハンディ画面にピッキングすべき製品のロケーション、数量が表示される(写真-3、4)。作業者は指示されたロケーションへ、電動移動ラックの通路を開けて進入、製品のバーコードを読んで確認してからパレットにピッキング(写真-5)。最後に1個に1枚荷札を貼るので、数量間違いも排除される(写真-6)。荷揃えが完了したら運送会社のドライバーがこれをトラックに積み込む。トラックが自社のターミナルへ出発するまでに、出荷情報は運送会社側にEDI送信され、送り状が出力されるという手はずだ。前日受注・翌日出荷が基本で、一部当日午前受注分まで当日出荷に対応している。
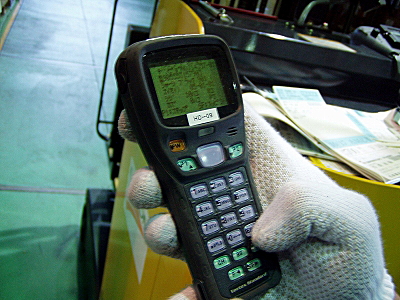
今回の「送り状レス化・セット作業レス化」によって、従来8人を要していたデリバリー作業担当者を7人に削減し、約1,000万円のコストを削減できた。 加えて、金額換算は難しいがトレース管理や配送状況問い合わせ対応の迅速化による顧客サービス向上も、大きな効果に数えられる。
滋賀工場の塩田義弘工場長は、「リーダーの村井が提出した課題に対し、ユーザックの担当者さんは問題点を探し出し、解決法を提案してくれました」とシステム構築を担当したユーザックシステムを評価する。 村井リーダーは、「ユーザックシステムの“送り状名人”を選定したポイントは、比較的安価なパッケージで求める内容に近い機能が得られるものだったこと。様々なカスタマイズ要求にも具体的に対応していただき、助かりました」と話す。 「今後はトレース管理システムを原材料側にも拡大し、トータルなトレーサビリティの仕組み構築に挑戦したいと思っています」
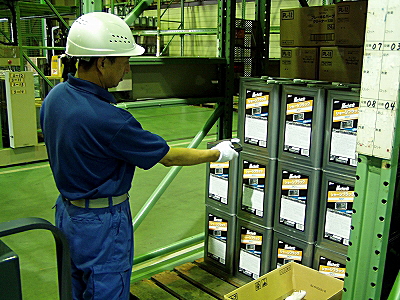
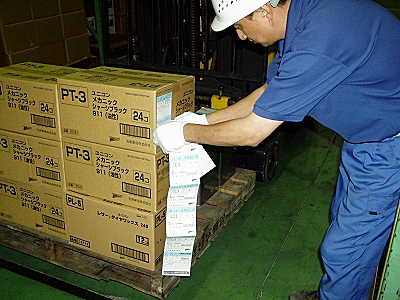
終着点なき物流改善に挑み続ける心意気。それを支えるシステムベンダーの使命もまた、大きい。
システム概念図
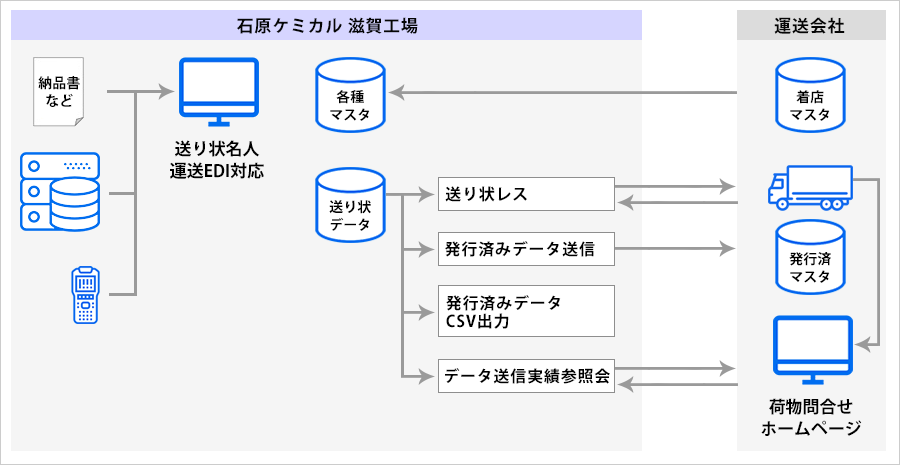